Dirt Ovals
Sign Up For Our E-News!Get info on exciting ticket offers, promotions and the latest info at The Dirty 'O'!


Date/Time | Event |
Saturday, May 29 Parking Lots Open: Pre Race Party: GA Gates Open: Show Time: | AMA Flat Track CHICAGO HALF MILE |
Saturday, July 24 Parking Lots Open: Pre Race Party: GA Gates Open: Show Time: | Team Demolition Derby |
Saturday, August 7 Parking Lots Open: Pre Race Party: GA Gates Open: Show Time: | All Wheels. Chicagoland's ULTIMATE car Show! |
Sunday, August 8 Parking Lots Open: Pre Race Party: GA Gates Open: Show Time: | All Wheels. Chicagoland's ULTIMATE Car show! |
Sunday, September 26 Parking Lots Open: Pre Race Party: GA Gates Open: Show Time: | Team Demolition Derby Racin for Boobs |
Frequently Asked Questions
Asphalt Oval Description: Hoosier produces a wide range of oval track asphalt tires to run from the ¼ bullrings to Super Speedways that repeats week after week. Custom Works RC10B5/RC10B6 Dirt Oval Adjustable Toe Rear A-Arm Kit. 1 review Average Rating:5.
QUESTIONS:
1. What is the number written on my bias race tire in yellow chalk?
2. Explain the use of Bleeder Valves.
3. How do Hoosier Open Wheel Dirt Compound Codes compare to the competition's codes?
4. What are some of the guidelines for Grooving and 'Siping' Late Model dirt tires?
5. Does it matter which direction I mount my Hoosier race tires?
6. What's the difference between grooving and siping my Hoosier dirt tires?
7. What are the do's and don'ts when storing Hoosier race tires at the end of the racing season?
8. What are the recommended operating temperatures of Hoosier sprint tires under various track conditions?
9. IMCA Air Pressure Siping & Grinding Tips
10. How do I groove and sipe my right rear sprint dirt spec tires?
11. How do I groove and sipe my northeast modified dirt tires?
ANSWERS:
1. What is the number written on my bias race tire in yellow chalk? As a result of a tire being bias in design (as opposed to radial), it will have a circumference that varies from tire to tire. This is not something that is unique to Hoosier but is common to all bias tire manufacturers. However, Hoosier has went to the expense of placing a 'chalk-mark' on its bias ply tires in an attempt to assist the consumer in making the proper selection when purchasing new tires. It is something Hoosier does that our competition does not. Now, to understand its use, you need to understand a little of the manufacturing process as well.
After a tire is cured, it is removed from the press and placed on a machine called a 'post-inflator'. On this machine each tire has air injected into it for a set period of time. The amount of air is determined by our engineering department and is not the same for every type of tire Hoosier produces. After a set time period, a tire is then measured and the circumference is recorded. Then a press operator writes the size on the side of treaded tires and on the tread of slicks, in yellow chalk. All Hoosier bias ply tires with a chalk-mark, follow this same process.
Now, how should the chalk mark be interpreted? It should be viewed as a reference point or a guide on purchasing tires by size to attempt to attain a certain stagger. Say for instance, you needed to replace your right front tire. Your car currently has 1' of stagger (with the RF @ 28 p.s.i.) but you want to get 1 1/2' of stagger. The tire you were replacing had an original chalk mark of 86', and had a roll out, of say, 85'. Obviously, you would want to purchase a tire bigger than the 86' tire you removed. Most likely, a tire with a chalk-mark of 86 1/2'. You have to remember there are many factors that go into what size a tire will actually measure. The ambient temperature that day, the air pressure in the tire, whether the tire is new or old. These are factors that no, one person, controls. You just need to be aware of their existence and work with what you know. The chalk mark does not tell you the circumference of the tire at running pressure, it does not tell you how big a tire will grow to, it tells you that a tire is either going to be bigger or smaller than another one with a different chalk mark. It's just that simple. Bias ply tires, by nature, are going to vary in size, whether you buy a Hoosier or the competition's tire. By keeping good records, using common sense and understanding how the chalk-mark Hoosier tires provide, you will be step ahead in selecting the proper sized tire(s).
2. Explain the use of Bleeder Valves.
General Notes
While racing you may see that your rear tire stagger may tend to change in an unfavorable manner (while using bleeders). It may seem to be unpredictable and uncontrollable. With careful bleeder valve Set Point Management, one can effectively minimize size control problems.
Main Reason Tires May Change Size
A common problem is to see the LR tire grow while the RR tire shrinks. This tendency occurs because the RR tire runs hotter than the LR tire, causing more air pressure gain, causing the RR bleeder to relieve more pressure (volume) than the LR bleeder.
Bias ply tires will change size when the air pressure changes. The higher the pressure, the bigger the tire. As a rule of thumb, the size change is linear with air pressure. A 10 psi change will either make the tire 1' bigger or 1' smaller (circumference). Each PSI is worth a .1' change in size.
Realize the use of Bleeder Valves limits the air pressure gain, but does not keep the pressure from lowering if the tire is allowed to cool. This is typically what happens during a caution period. This is when many will notice trouble with their race car handling. Why? There is no system to replace the lost air pressure.
Bleeder Valve Recommendations:
1) Use Bleeder Valves to REDUCE the air pressure buildup, not eliminate it:
Bleeders should not be used to maintain a constant air pressure. You must always set the bleeder higher than the starting cold air pressure. If your tires cool (caution period), the inflation pressure will be reduced by the amount of pressure the bleeder valve bled off. It is normal to see 7-8 psi of RR buildup (without bleeders). If the bleeders kept the RR tire at a constant pressure hot (no buildup), your car will lose .7 to .8' of stagger if the tires are given time to cool. This is not due to RR tire shrinkage, this is due to LOW AIR PRESSURE. You may be compromising driver safety.
2) Recommended Initial Bleeder Valve Set Points:
LEFT REAR: + 3 psi over cold
RIGHT REAR: + 4 to + 6 psi over cold
LEFT FRONT: bleeders generally not needed due to lack of tire heat
RIGHT FRONT: + 5 psi minimum if used
NOTE: The use of bleeders on the Right Front tire is not recommended by tire manufacturer on higher banked tracks. Reducing air pressure reduces the strength of the RF (any) tire. Bleeders may allow the RF (or any) tire to operate below the minimum safe recommended cold air pressure. You should never allow this to happen. Bleeders may be used more successfully on flat tracks to control car handling by reducing RF pressure gains.
3) Axle mounted Bleeder Valves need higher set points than wheel mounted bleeders:
If you had a 'system' that worked with wheel mounted valves, it may not work anymore. You will have to modify your thinking. This is due to the fact that axle mounted valves are more efficient at bleeding off air pressure gains. You should start off with more air pressure cold (try +2 psi) and then set you bleeders based off this higher starting pressure. Start with these settings and make adjustments as needed. They will vary depending on the race track, driving style & car handling.
Adjustment example:
Let’s say you run an initial Bleeder Valve setup & RR comes in 1/4' smaller than it was cold, but the LR stayed the same, in which the net loss of 1/4' stagger is not desired. You have a few options available to you which will fix the stagger. They are:
1) Set LR bleeder 2 psi lower.
This allows the LR bleeder to release 2 psi more, which should make the LR tire about 1/4' smaller than before, making both rears - 1/4' hot.
2) Leave the LR alone & Set RR bleeder 2 psi higher.
This should allow the RR tire to grow 1/4' also, keeping the stagger (and sizes) the same.
3) Leave the LR & RR bleeders alone (+3 LR,+5 RR), but lower RR cold air pressure 2 psi.
This increases the gap between RR cold and bleeder set point to +7 psi
In this case, the RR tire cold will be 1/4' smaller than it was before, but it will be 1/4' bigger hot than it was before.
NOTE: Realize that there are several ways to fix the problem & that all we are doing is changing the gap between the cold air pressure setting and the bleeder valve set point. It is personal preference as to how you get there, realizing that you are changing the car's handling when you adjust air pressures.
3. How do Hoosier Dirt Oval Compound Codes compare to the competition's codes? This is a guide to assist you in comparing compounds; your best guide is your own 'at the track' durometer readings. But here is a chart listing rough comparisons.
Hoosier Racing Tire
Midget/Micro Dirt/ATV Flat Track
Compound Cross Reference Chart
Scale | Hoosier Compounds | Competitor |
---|---|---|
SOFT | D10 | SD23 |
- | RD12 | SD30 |
- | D12 | SD33 |
- | RD15 | SD35 |
- | D15 | SD38 |
- | RD20 | SD40 |
- | D20 | SD44 |
- | D25 | SD48 |
- | KS1* | MD50 |
FIRM | ASCS2*, POWRi* | HD57 |
Dirt Oval Street Stock Rules
Sprint Dirt
Compound Comparison Chart
Scale | Hoosier Open Comp | Hoosier Spec | Competitor |
---|---|---|---|
SOFT | D10 | SD23 | |
- | RD12 | SD28 | |
- | D12 | H12 | SD33, MC1 |
- | RD15 | SD35 | |
- | D15 | H15 | SD38 |
- | RD20 | MC2, SD44 | |
- | D20 | SD48 | |
- | D25 | MEDIUM** | MD50, MC3 |
- | DT3* | ||
- | HARD | MD56 | |
- | F85A | HD65 | |
FIRM | F95 | HD70 |
Dirt Ovals In North America
Late Model/E-Mod
Compound Comparison Chart
Rfactor Dirt Ovals
Scale | Hoosier Open | Hoosier Spec | Competitor |
---|---|---|---|
SOFT | 1110 | SD23 | |
- | 1200 | SD33, SD38 | |
- | 1300 | Soft | |
- | M20, D40, FT200 | SD44 | |
- | 1325 | MED. 100, USA25 | |
- | 1350 | USA21, HTS1350 | |
- | 1400 | MED. 200 | SD48 |
- | 1425 | ||
- | 1450 | M30s, MED, A40s, M500, W30s | MD57 |
- | A40, FT400 | ||
- | USA55, HTS1600 | ||
- | 1600 | M40, WRS-2 | MD56 |
- | W70 | 35-W, Hard | KK704 |
- | IMCA, H500 | ||
FIRM | D70 | H40 | HD70 |
4. What are some of the guidelines for Grooving and Siping Late Model dirt tires?
(Answer compiled with the assistance of driver Scott Bloomquist)
The one thing every racer has to remember is that the tires are the only link between the chassis, engine and track, and an otherwise perfectly set up race car can not perform up to it's potential.
Dirt racers have to pick the right tire compound much like an asphalt racer, but there is another important step to getting the most out of a dirt tire. Dirt racers often have to alter the design of a tread pattern to best work with the conditions at a particular track, on that day and with their driver's style or habits. We can't tell you exactly the specific kind of grooving that will work best for your situation, but we can provide basic information to make you better able to decide for yourself as you encounter different racing conditions.
We also have to consider the abrasion of the track, how wet or dry the track is and if the track contains rocks or other debris that will tear up the tire. All of these conditions must be considered when deciding on what kind of groove to use, how deep to cut and how many grooves can be out without causing the early demise of the tire. Along with these factors racers must consider the amount of heat a track puts in their tires. In addition to enhancing traction, grooving helps the tire dissipate heat and can be used to help control tire temperatures.
Grooving and Wear
Any time a groove or sipe is cut into a tire it accelerates wear. The trick is to balance the benefit of grooving with the increased wear. One of the reasons we sipe a tire is to prevent the tread surface from glazing over and becoming slick. Sipes keep the surface wearing and the tire working throughout the race. (see photo)
Learning to recognize the amount of wear you can expect from a track not only helps you choose the right compound tire for the night but is important information for deciding what pattern and depth grooving to use. The object is to maintain the highest level of traction throughout the race without wearing the tread off of it with five laps to go.
With an understanding of the basics of grooving tires racers will be able to look back on their experience with the tracks they have raced on and make better decisions on what type of grooving will help them most. Keeping records of the results of your decisions is the best teacher, so if you are not already keeping a 'book' on each track, start one now.
Soft Tires
Racers rarely run soft tires in a race, especially the 100 lap events, but grooving soft tires correctly can be a big help in qualifying or short heats on a wet track. Softer tires are generally used on tracks that have a lot of moisture but not a lot of abrasion. You may also use a soft tire on a surface that does not generate a lot of heat in the tire and may have loose dirt or clay on the surface throughout the race. Cutting more grooves can help clean away loose dirt, plus improve traction because of the increased number of edges available to dig into the tracks surface. On tracks where you are not moving or throwing any dirt, but the surface is still relatively soft, a soft tire can often be run effectively with little or no grooving at all.
Keep in mind that grooving not only increases traction, but increases the rate at which a tire wears. A soft tire will begin losing it's traction sooner as the amount of grooving increases. The softer material naturally tears easier and fatigues sooner, causing the tire to slow down. On a surface with a lot of traction or if it contains rocks and other debris, the tire will tear up much quicker with excessive grooving. Determining the correct amount and style of grooving comes with experience and watching how the tire wears and what the driver felt s the race goes on.
One of the things we do with soft tires is only groove about half way across the blocks to prevent weakening the structure too much. (see photo) With the large stagger block tread design we can often run that tire with little or no additional grooving, depending on the condition of the track. Usually we will run that pattern on all four corners on a wet track.
Occasionally when we run a ribbed tire on the right rear and do the grooving ourselves, we will follow the groove lines the factory put on the tire and then wait to see if the tire is going to start tearing and how many laps it takes for the tire to start working well. If the tire needs a couple of laps before it starts working we may add some grooves or sipes to give the tire a little extra grab until it develops enough heat to work on it's own.
Hard Tires
Though some harder tires may withstand grooving better than the soft compounds, the track conditions that made you choose a hard tire may not require much in the way of grooving. In the South we often do not groove the harder tires much at all. In fact, there are some tracks that pack down to where they are similar to asphalt and we have run tires with no grooves at all. We leave the tires full slick.
Grooving the Tread 'Shoulders'
Grooving the shoulders can be helpful if you plan to run the high line or on a cushion and need to be moving some dirt. Grooves on the shoulders help clean away some of the loose dirt to get at moisture beneath it. Sometimes the outer row of blocks is also grooved on the right rear to work with the shoulders.
On some of the harder natural rubber tires we sometimes sipe the shoulders. This can really help when you are rolling the tire under when running lower tire pressures on a very slick track. The sipes can help prevent the shoulder area of the tire from glazing over and losing traction. The shoulder is as important a part of the tire as anything else and if you are going to be running on it due to low air pressure or because you are running against the cushion you need to make the best use of it.
Grooving Widths
Some tracks do not have a lot of abrasion to them and edges on the tire can increase traction considerably. When we get on a surface like that we will use wider grooves to present a cleaner, more prominent edge to the racing surface. Narrow grooves may not have enough distance between edges to allow them to work properly.
On some tracks you can groove the tires twice as much with a narrow groove, or half as much with a wide groove and accomplish the same thing. It depends on the track surface and how abrasive it is or if it contains rocks that will tear the tire up. You don't want a lot of grooves on a rocky or highly abrasive track. Fewer, but wider grooves stand up to these harsher conditions better.
Shapes of the Grooves
There are three basic shapes used in grooving: square, V, and sipes. Square grooves are the same width through it's entire depth. V grooves start out wide at the top and taper to nothing at their bottom. Sipes are thin slits cut by installing the blade upside down in the holder and using the separate ends of the blade to cut slices in the tire.
All three types of grooves can be used in various depths depending on conditions and the length of the race. The V groove is often used when the track is expected to need more tread contact later in the race. As the tire wears, the grooves become smaller or disappear completely. Square grooves can be used the same way but the extra width could provide enough leverage for an abrasive track to tear the tire if the track becomes abrasive.
Siping is usually meant to make the tread more pliable and does not produce the edges square or V grooves do. Siping also helps the tread maintain a more consistent wear that helps keep the tire working uniformly.
Grooving Angles
The angle at which grooves are cut determines how much of the edges are exposed to the track when the car is in various degrees of slide. Dirt race cars seldom if ever run in a straight line but the driver will try to keep the car much straighter when the track is slick than when there is a lot of bite to work with. When the track is slick we keep the grooves pretty straight. But when we spend a lot of time with the car sideways we put more angle into the grooves.
How much of an angle is dependent on the drivers style and experience is the only way to determine the best angle for your situation. The idea is to keep the maximum amount of the tires edges facing the direction the tire is actually traveling. As a dirt car travels around the track on a given line, the body is actually pointed towards the infield a certain number of degrees. If the driver is consistent you can determine an angle for the tire grooves that will work best for your combination.
Circumference Grooves
We almost always cut circumference grooves in our front tires because they help make the tread blocks more flexible which increases traction and helps the steering. Here also the width of the groove is determined by individual track conditions.
At some tracks we will also sipe across the circumference grooves so that we are making little blocks that are more flexible yet. These smaller blocks can help a lot when you catch little rough areas on the track.
Rough Race Tracks
We have found that as the roughness of a track increases, so does the need for grooves. Unless the track surface is very smooth, some sort of grooving is likely to be necessary to be fast. When you groove a tire more, it makes the tread surface much more flexible. It can then follow or shape itself to the surface much better to provide the maximum amount of bite possible.
Grooving and Heat
Some tracks naturally put a lot of heat into a tire and can actually cause the tire to melt or blister. On these kinds of tracks we have found that grooving helps cool the tire. The grooves (and sipes) help move air across the tires surface which keeps the tread temperatures down. Grooving also produces more surface area which helps transfer the heat out of the tire to the air. You have to balance grooving with the amount of abrasion or traction available because tracks that generate a lot of heat may also be very abrasive or contain rocks that want to tear the tire up if it is grooved too much. Too much grooving or siping on a high traction (or abrasive) track can cause the tire to start tearing up very early in the race.
To help a tire dissipate heat without weakening the tread blocks too much we will cut grooves in the center of each block instead of cutting all the way across it. We have even made a tool for drilling a circle in the middle of individual blocks to help cool without weakening the blocks structure too much. This kind of grooving works well when you want as few grooves as possible for speed but need to increase cooling to prevent blistering.
Race Length
The number of laps to be run is an important consideration when deciding how to groove your tires. Softer tires may be used in shorter races of 25 to 40 laps and you will have to be careful about removing too much rubber which may cause the tire to wear out prematurely. Accelerated wear caused by excessive grooving can be a problem with harder tires normally used in 100 lap races depending on how abrasive the track is.
We try to decide how much wear we expect on a particular track, then adjust our grooving accordingly. Often we will groove only half way into the depth of the tread so as the races progresses and the track turns smooth and abrasive normal tire wear produces very shallow or grooves that begin to disappear. Then when we need the most rubber on the track, the grooves are just about gone.
Keeping Records is Vital
Learning the tracks on which you race and how they change over the course of an evening of racing will go a long way in helping you learn to groove tires. Keep track of how your last grooving ideas worked with the condition of the track surface. What were the other guys doing that drove past you? Read your tires after the race to see if another style or amount of grooving would have worked better, then write it down so you will have that information the next time you are in a similar situation.
Much of learning to prepare and drive on dirt surfaces comes from experience and applying that information to your current situation. You may spend some time writing down what DIDN'T work, but that puts you closer to what WILL work to make you faster.
5. Does it matter which direction I mount my Hoosier Racing Tires? All Hoosier tires having directional arrows must be mounted so that the tire travels in the direction of the arrow. Hoosier tires having directional arrows will have them on both sidewalls. Directional arrows may not be on a tire that can have both a left and/or right side application. All Hoosier tires not having directional arrows should be mounted as detailed below.
Every Hoosier race tire has a four character serial code embossed into ONE sidewall of the tire. All Hoosier DOT tires will also have two additional codes as required by the Department of Transportation. (Example: J7AB 4AX8 3701)
MOUNTING GUIDELINES FOR TIRES WITHOUT DIRECTIONAL ARROWS
CIRCLE TRACK RACING TIRES:
Dirt Track Tires:
Hoosier tires must be mounted with the serial code located toward the infield for the first night of competition. After the first night, you are welcome to flip the tire on the wheel to extend tread life.
ROAD RACING TIRES:
(Includes catalog numbers beginning with 43, 44, 45, 46)
In most cases, Hoosier tires used in Road Race applications should be mounted with the serial code toward the center of the vehicle. Once a tire has been run in the proper orientation it is acceptable to remount the tire in the opposite direction to even out the wear.
DRAG RACING TIRES, INCLUDING DOT DRAG TIRES:
(Includes catalog numbers beginning with 17, 18)
Hoosier drag tires can be mounted to rotate in either direction. Hoosier drag tires can also be flipped or reversed to provide even wear. 6. What is the difference between grooving and siping my Hoosier dirt tires? View Difference Here7. What are the do's and don'ts when storing Hoosier race tires at the end of the racing season?
The useful life of a tire, whether mounted or dismounted, is directly affected by storage conditions. Tires should always be stored indoors in a dark, cool, dry room.
DO
1 Remove the tires from the vehicle.
2. Remove the air from the tires and store them on their side in a cool/dark/dry environment.
3. Place tires in a black plastic bag when stored during the 'off-season'.
4. Make sure the temperature range in the storage location is between 40-90 degrees Fahrenheit.
DON'T
1. Don't store tires in direct sunlight or near electric motors. (Electric motors emit small amounts of ozone.) Tires need to be protected from light, especially sunlight. Light causes ultraviolet damage by breaking down the rubber compounds. The storeroom should not contain electrical welding or any other equipment that could produce ozone.
2. Don't apply any chemical treatments to Hoosier tires. (It's not necessary and may actually damage the integrity of the tire by breaking down the rubber properties of the tire.) Tires must not be allowed to come in contact with oils, greases, solvents, or other petroleum products that cause rubber to soften or deteriorate.
3. Don't store tires in sub-freezing temperatures for any length of time. (The rubber can freeze and may crack as a result.) 8. What are the recommended operating temperatures of Hoosier sprint tires under various track conditions?
Optimum temperature ranges for Hoosier Sprint tires:
The following is a table with temperature limitations for Hoosier Sprint tires. Please keep in mind that there are a number of variables that must be taken into account when taking tire temperatures. Some of these variables are:
1. Needle pyrometer vs. surface pyrometer vs. infrared pyrometer. The temperatures listed are from a needle pyrometer. Surface pyrometer readings will be 10 to 20% lower than needle readings. Infrared pyrometer readings should be close to surface pyrometer readings provided that the distance from the pyrometer to the tire is in the range designed for the pyrometer being used. This distance is typically about 6-8'.
2. The time between being at full speed on the track and taking the reading. This variable is very hard to factor out. If tire temps are high and the ambient temperatures are low the tire will cool very fast and your temperature readings will be misleading.
3. Location on the tire. This includes which row of blocks on the tire and where in the block you are checking. It is best to always check the same rows. It is also best to stay at least 3/8' away from a groove or heat dissipation vent. Temperatures on the first inside row and the outer 2 rows of a 105/18 should be excluded. On left rears, the 1st inside and 1st outside rows should be excluded.
4. The amount of wear the tire sees: As tread rubber wears down there is less mass to heat up so tire temps will be lower.
5. Pyrometer calibration.
These are temperature readings taken within 3 to 4 minutes after the car is at full speed on full tread depth non-grooved tires. If tire temps are below the minimum listed the tire will be slow to fire. If tire temps are above the maximum listed the tire will slow down due to fatigue or blistering. The average temperature of the tire should be within the ranges listed below. If one row on the tire is running hotter than the listed ranges try grooving that row in a circumferential direction.
-D10 ambient temp up to 200°F
-RD12 ambient temp up to 220°F
-D12 160°F up to 250°F
-RD15 160°F up to 230°F
-D15 160°F up to 260°F
-D20 180°F up to 260°F (unless it is a high wear situation)
-F55 200°F up to 280°F
A good balance between left rear and right rear tires is also important. A good rule of thumb is that the left rear should be around 20-30°F cooler than the right rear. One exception is a high speed, high banked track like Eldora. At Eldora we typically see LR temps about equal to RR temps.
A common pitfall is that if the tires are running too hot it is not always the best thing to run a harder tire. A harder tire provides less traction (except F55) and will spin more which in turn will make it run hotter. Sometimes a softer tire will hook the car up better or grain a little. Both of these conditions will make the tire run cooler.
With 'RD' type tires being high traction tires for dry slick tracks and 'D' type tires being for high heat, high speed tracks these are a few of the most common combinations:
'D' LR and 'D' RR (Eldora-type tracks)
'RD' LR and 'D' RR (Lincoln Speedway or Williams Grove Speedway when the track is fast)
'RD' LR and 'RD' RR (Lincoln Speedway or Williams Grove Speedway when the track is slow) 9. IMCA Air Pressure Siping & Grinding Tips
1) What is the proper air pressure for the IMCA tire?
a. Temperature profile across the tire is the best indicator
- If your temperatures are even across the tread, your pressures are correct
b. We always recommend running the most pressure possible
- Under inflated tires will feel soft, squirmy, unresponsive
- Over inflated tires will be loose with little traction, “on top of the track”
c. Standard IMCA Modified setup:
- Heavy Track - 15 psi right side, 12 psi left side
- Slick Track – 14 psi right front, 10 psi left front, 13 psi right rear, 10 psi left rear
2) How should I sipe my IMCA tires?
a. Why do we sipe?
- To build or remove heat
1. We sipe across a tire to increase wear and build heat. We sipe around a tire to reduce heat and increase sidebite when additional traction is not necessary.
- Reduce block stiffness and increase wear on tires too hard for track conditions
b. Siping tips
- We generally never sipe more than ½ depth of any block. 1/3rd the depth of the block, or 3/32nds, is preferred in most situations.
- The more sipes you apply, the shallower they should be. In turn, the less sipes you use, the deeper you can cut while still minimizing the risk of chunking.
- The more evenly you can space your sipes within a block, the better their performance will be. You should always try and limit the amount of small, unsupported corners of a block to reduce tread chunking.
- Unless facing severe track conditions, IMCA tires seem to like aggressive siping, both across and around, the tire. In turn, if the track is severe, only shallow, circumferential sipes should be used to help reduce temperature and possible tread blistering. Taylor your quantity and location of sipes to the track conditions; the easier the track, the more sipes and vise versa.
3) What is the best siping tool to use?
a. I have no preference on how sipes are created. All the tools I have seen accomplish the goal, it just depends on what your budget will allow. I personally use a 4-8 blade unheated hand siper available from many IMCA parts suppliers.
4) When and how should I grind my tires?
a. I prefer a light grit sanding disk on a variable speed, high torque grinder. I am only looking to remove the surface “shine”, not cut away layers with my grinder. If you see smoke while grinding, reduce your grinder speed or disk grit.
b. Generally, I prefer to sand/grind before I sipe to assure my sipes maintain their attended depth.
c. I would much rather sipe and sand a tire than use one of the aggressive grinding disks currently in use. There is very little control on depth, size, and location of the “sipes” created by these grinders. 10. How do I groove and sipe my right rear sprint dirt spec tires?
104/16-15 RaceSaver
105/16-15 MED (High Heat Track Conditions)
105/16-15 MED (High Heat Fast Track Conditions)
105/16-15 MED (Extreme Heat, 1/2-Mile Tracks)
105/16-15 MED (Slick Track Conditions, Not Abrasive Surface, Minimal Heat)
105/16-15 H15, H20 (Normal Track Conditions)
105/16-15 H15, H20 (Medium Heat Track Conditions)
105/16-15 H15, H20 (High Heat Track Conditions)
Rear Tire (High Heat Conditions)
Left and Right Rear
Rear Tire (Slick Conditions)
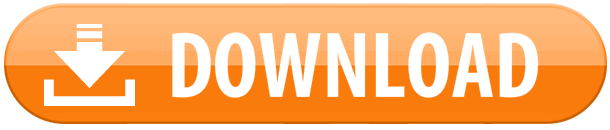